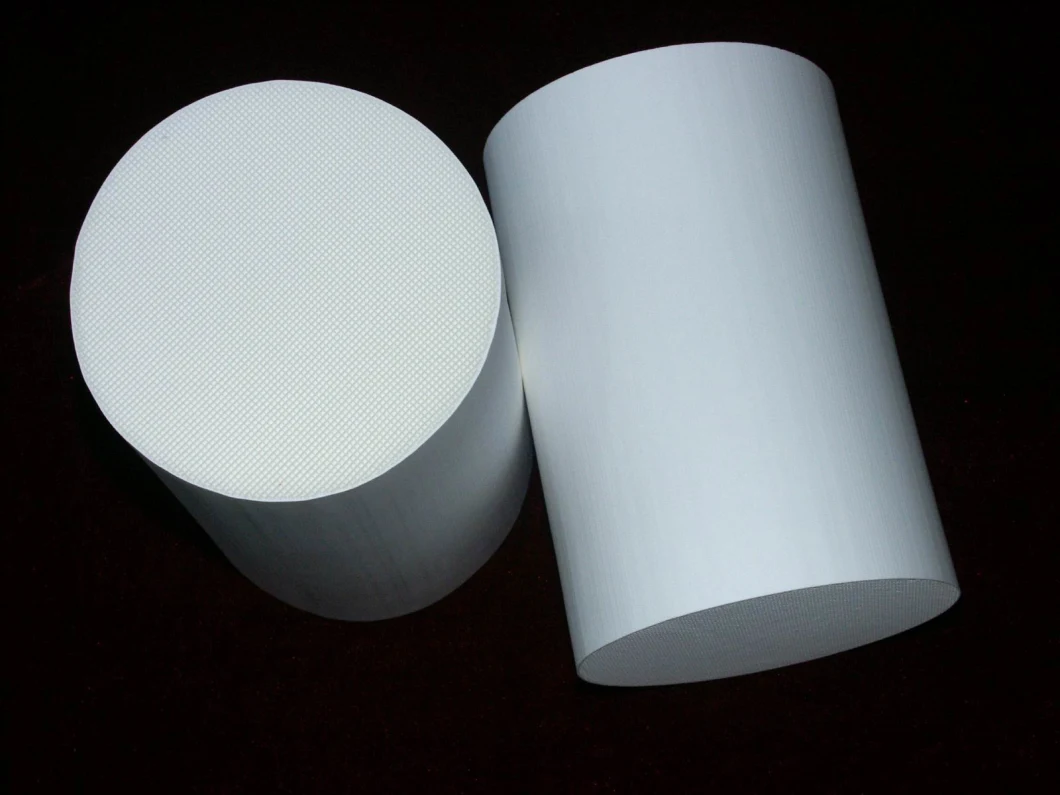
Cordierite Ceramic Honeycomb Substrate is used as catalytic converters of gasoline engines, the honeycomb ceramic catalyst substrates are coated by catalyst. At the same time, we improve the specific surface areas and cut down the heat capacity to increase the catalytic function. When the noxious emissions pass through, HC, CO and NOX will be converted into harmless components.
The necessary property of honeycomb ceramic catalyst substrate used in cars as follows:
*High specific surface area: Ensure exhaust gas could contact weigh catalyst enough
*Stable water absorption: Guarantee catalyst could be firmly and evenly coated on the surface of substrate, so it's no waste for too thick coating
*Warm up characters: After starting up engine, the temperature of substrate could reach the active temperature of catalyst in the shortest time
*Low exhaust resistance: Ask exhaust resistance of substrate to engine low, so that it won't affect the performance of engine
*High intensity: Substrates work in bumpy cars, so the intensity of substrates must be too high to be destroyed
*Perfect assembly: Substrates are parts of exhaust; Perfect appearance and exact dimension could ensure assembly perfect.
The preferred catalyst support structure is a honeycomb configuration which includes a variety of unobstructed parallel channels sized to through gas flow and bounded by thin ceramic walls. The walls of these channels provide the surface for precious-metal catalysts that convert noxious emissions into carbon dioxide, nitrogen and water vapor. We can provide honeycomb ceramic substrate has been coated and non-coated precious-metal. Our Honeycomb ceramic is made of cordierite, The cells density can be 100 cpsi, 300 cpsi, 400 cpsi or 600 cpsi. The usual cpsi (Cell Per Square Inch) for catalytic converter substrate is 400, the shape of ceramic converter substrate is round, racetrack, ellipse and other special shape according to the customer's requirement.
Features:
*Low thermal expansion
*High surface area
*Long-term durability performance.
*Low pressure drop.
*Good thermal shock resistance
*Combined with the EGR systems to help different vehicles to satisfy emission standard
*Low light-off temperature
*Excellent adhesion between wash-coat and susbstrate with netty structure
Chemical composition | ||||||
Property | Unit | Value | ||||
SiO2 | % | 48-51 | ||||
Al2O3 | % | 31-34 | ||||
Fe2O3 | % | <1.0 | ||||
MgO | % | 12-14 | ||||
K2O+Na2O | % | <1 | ||||
Others | % | <1.0 | ||||
Physical properties | ||||||
Property | Unit | Value | ||||
Compressive Strength | A axis | MPA | ≥10 | |||
B axis | ≥1.4 | |||||
C axis | ≥0.2 | |||||
Water adsorption | °C | ≥17 | ||||
Bulk Density | g/cm3 | ≤0.5 | ||||
Softening temperature | °C | ≥1360 | ||||
Thermal Expansion °C-1(20-800°C) | °C | ≤1.2×10-6 | ||||
Thermal Shock Resistance | -- | Not crack after 3 cycles (30 mins) |
Channel density | Shape | Dimensin (mm) |
400cells/square inch2 | Round | Φ150 x100 |
Φ144 x152.4 | ||
Φ118 x152.4 | ||
Φ115.4 x152.4 | ||
Φ106 x100.4 | ||
Φ103x100 | ||
Φ101.6x152.4 | ||
Φ100x100 | ||
Φ93 x152.4 | ||
Φ83 x152.4 | ||
Φ80x100 | ||
Φ76x50 | ||
Φ41x25 | ||
Racetrack shape(ellipse) | Φ169 X 85.7 x115 | |
Φ169 X 80.8x115 | ||
Φ148 X 84x152.4 | ||
Φ144.8 X 81.3 x152.4 | ||
Φ127 X 63.5x152.4 | ||
Φ93 X 61x90 | ||
Φ120 .6X 80 x152.4 | ||
Φ143 X 98x152.4 | ||
Φ147 X 95x152.4 | ||
Φ177.8 X114.3x170 | ||
Special shape | 144x84x75 | |
114x105x115 | ||
120.2x108.2x75 | ||
112.2x92x115 | ||
119.5x99.5x115 | ||
122.3x104.4x80 |