Metal Honeycomb Converters substrate
Metallic substrate is with the advantages of fast burning, small volume, high mechanical strength, prominent heat-resistance, etc. It is widely used in exhaust gas purification, especially for motorbike. Firstly metallic substrate should be pretreated in order to generate a transition layer which is required to solve the mismatched heat expansion between metallic substrate itself and the active layer. On the transition layer, it is coated with rare earth catalyst, while in active layer is coated with noble metal like Pt, Pd, Rh.
It satisfies the Euro II III V standard. Features:
Applications: Transforms CO, HC and NOx to CO2, H2O and N2
Chooses metal catalyst with suitable size, volume, precious metal content and ratio according to motorcycles' practical situation to satisfy certain emission rule
We always choose metal honeycomb carrier with stainless steel crust and Fe-Cr-Al core made
Features:
*Low thermal expansion
*High surface area
*Long-term durability performance
*Low pressure drop
*Good thermal shock resistance
*Combined with the EGR systems to help different vehicles to satisfy emission standard
*Low light-off temperature
*Excellent adhesion between wash-coat and susbstrate with netty structure
*Excellent quality and competitive price
*Stainless steel shell,
*Foil material is OCr21Al6, foil thickness is 0.1mm
*Cell pieces per square inch: 100, 200, 300 and 400cpsi
*Shape and dimension is customized according to drawing provided
Major technical parameters:
Substrate: Metal honeycomb substrate (Fe-Cr-Al alloy)
Light-off temperature: CO≤ 200° C, HC≤ 200° C, NOX≤ 200° C
Coating losing rate ≤ 3%
Conversion rate: CO≥ 90%, HC≥ 90%, NOX≥ 80%
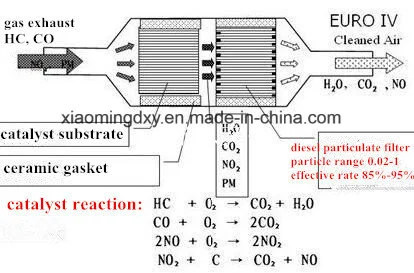
Working principle
*Catalytic converter is a device used to reduce the toxicity of emissions from an internal combustion engine.
*Reduction of nitrogen oxides to nitrogen and oxygen:
2NOx xO2 + N2
Oxidation of carbon monoxide to carbon dioxide
2CO + O2 2CO2
Oxidation of un-burnt hydrocarbons (HC) to carbon dioxide and water
CxH2x+2 + [(3x+1)/2]O2 xCO2 + (x+1)H2O
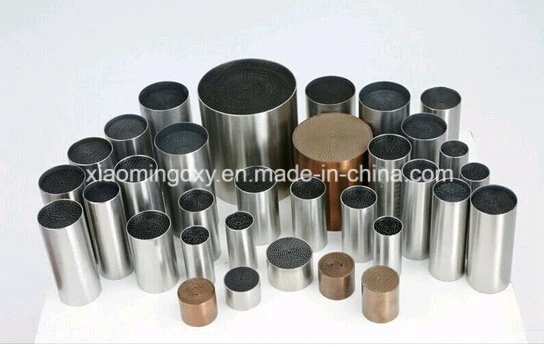
Metallic substrate is with the advantages of fast burning, small volume, high mechanical strength, prominent heat-resistance, etc. It is widely used in exhaust gas purification, especially for motorbike. Firstly metallic substrate should be pretreated in order to generate a transition layer which is required to solve the mismatched heat expansion between metallic substrate itself and the active layer. On the transition layer, it is coated with rare earth catalyst, while in active layer is coated with noble metal like Pt, Pd, Rh.
It satisfies the Euro II III V standard. Features:
Applications: Transforms CO, HC and NOx to CO2, H2O and N2
Chooses metal catalyst with suitable size, volume, precious metal content and ratio according to motorcycles' practical situation to satisfy certain emission rule
We always choose metal honeycomb carrier with stainless steel crust and Fe-Cr-Al core made
Features:
*Low thermal expansion
*High surface area
*Long-term durability performance
*Low pressure drop
*Good thermal shock resistance
*Combined with the EGR systems to help different vehicles to satisfy emission standard
*Low light-off temperature
*Excellent adhesion between wash-coat and susbstrate with netty structure
*Excellent quality and competitive price
*Stainless steel shell,
*Foil material is OCr21Al6, foil thickness is 0.1mm
*Cell pieces per square inch: 100, 200, 300 and 400cpsi
*Shape and dimension is customized according to drawing provided
Major technical parameters:
Substrate: Metal honeycomb substrate (Fe-Cr-Al alloy)
Light-off temperature: CO≤ 200° C, HC≤ 200° C, NOX≤ 200° C
Coating losing rate ≤ 3%
Conversion rate: CO≥ 90%, HC≥ 90%, NOX≥ 80%
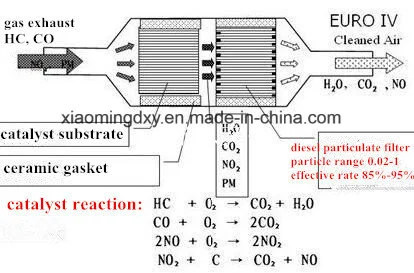
Working principle
*Catalytic converter is a device used to reduce the toxicity of emissions from an internal combustion engine.
*Reduction of nitrogen oxides to nitrogen and oxygen:
2NOx xO2 + N2
Oxidation of carbon monoxide to carbon dioxide
2CO + O2 2CO2
Oxidation of un-burnt hydrocarbons (HC) to carbon dioxide and water
CxH2x+2 + [(3x+1)/2]O2 xCO2 + (x+1)H2O
Light-off temperature | Durability | Conversion efficiency | Coating desquamate rate |
CO ≤ 230 HC ≤ 260 NOX ≤ 250 | 1000KM | CO ≥ 85% HC ≥ 80% CO ≥ 85% | ≤ 7% |
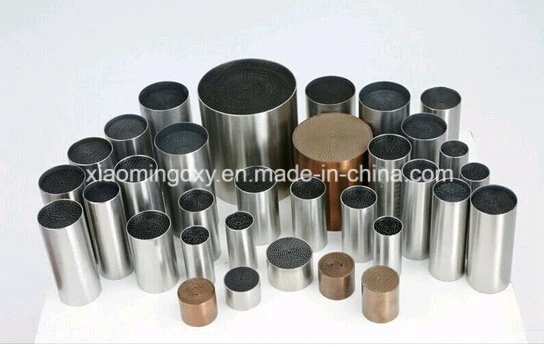
Shape | Shell size(mm) | Core size(mm) | Cell density (CPSI) |
Rotundity | Φ 30 × 22 | Φ 28 × 20 | 100/200/300/400 |
Rotundity | Φ 35 × 20 | Φ 33 × 20 | 100/200/300/400 |
Rotundity | Φ 35 × 30 | Φ 33 × 30 | 100/200/300/400 |
Rotundity | Φ 35 × 40 | Φ 33 × 40 | 100/200/300/400 |
Rotundity | Φ 35 × 50 | Φ 33 × 50 | 100/200/300/400 |
Rotundity | Φ 35 × 60 | Φ 33 × 60 | 100/200/300/400 |
Rotundity | Φ 35 × 70/100/130 | Φ 33 × 60/90/120 | 100/200/300/400 |
Rotundity | Φ 42 × 70/100/130 | Φ 40 × 60/90/120 | 100/200/300/400 |
Rotundity | Φ 45 × 70/100/130 | Φ 43 × 60/90/120 | 100/200/300/400 |
Rotundity | Φ 63,5 × 85/100/130 | Φ 60,5 × 74,5/90/120 | 200/300/400 |
Rotundity | Φ 73 × 70/100/130 L | Φ 70 × 60/90/120 | 200/300/400 |
Rotundity | Φ 93 × 70/100/130 | Φ 90 × 60/90/120 | 200/300/400 |
Rotundity | Φ 100,3 × 100/130 | Φ 98,3 × 90/120 | 600 |
Rotundity | Φ 144 × 150/152,4 | Φ 142 × 140/142,4 | 200/300/400 |
Rotundity | Φ 190 × 200 | Φ 188 × 190 | 200/300/400 |
Rotundity | Φ 420 × 100/130 | Φ 416 × 90/120 | 300/400 |
Race track | 123 × 63 × 85 | 120 × 60 × 75 | 200/300 |
Race track | 123 × 63 × 100 | 120 × 60 × 90 | 200/300 |
Race track | 78,5 × 52 × 104 | 76,5 × 50 × 90 | 200/300 |