Honeycomb Ceramic Substrate Description:
Honeycomb ceramic substrate is new developed ceramic part.
Because of it's features of corrosion resistances, large specific surface area, small heat resistance, good thermal conductivity and excellent thermal-shock resistance, fast heat exchanging and energy saving. It's widely used in car/vehicle, motorcycle etc catalytic converter.
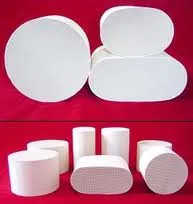
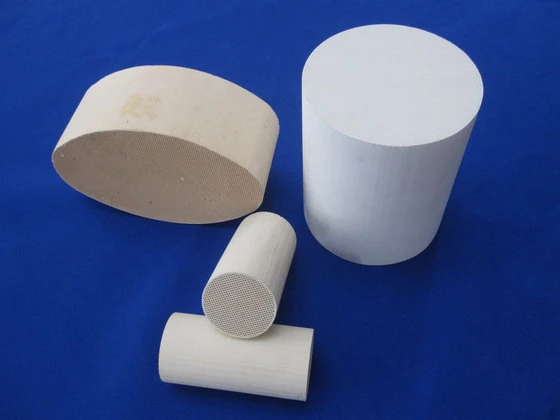
Specification
*Density: 1.7~3.8g/cm3
*Thermal expansivity: 1.5~5.0× 10-6/° C(20~100° C)
*Thermal conductivity: 1.2~3.0w/m. K(20~1000° C)
*Wall thickness: 0.8~1.5mm
*Compression strength: >50Mpa
*Heat exchange surface normal temperature: 300~500m2/m3
*Max Temperature: 1300~1400° C
*High working temperature
*Large specifc surface area
*Good thermal conductivity
*All shapes avalible
Application
*As support of catalyst, ceramic honeycomb materials are typically used for purifying automotive emission, removing bad smell etc, for instance, utilized in exhaust catalytic converter, air- fresher machine for hotel, restaurant, toilet and so on.
*Heat transfer agent: It can save 12% of energy in heat exchange, and it mainly utilized in heat recovery unit of RTO. Refractory stove: Low mass/volume, fast heat conduction. Gas burn distributing plate: Complete burn, energy saving is 10%.
*As filtrate substrate, they are generally utilized in food processing, environmental industry, metallurgical industry etc. For filtering particulate in industrial waste gas and bubble in liquid of molten melt and making the molten melt laminar so as to increase casting yields, also filtering impurities in juice, dextrose and sucrose etc.
Features:
*low thermal expansion
*large specific heat capacity
*high specific surface area
*low pressure drop
*small thermal resistance
*good thermal conductivity
*good heat-shock resisting ability
Honeycomb ceramic substrate is new developed ceramic part.
Because of it's features of corrosion resistances, large specific surface area, small heat resistance, good thermal conductivity and excellent thermal-shock resistance, fast heat exchanging and energy saving. It's widely used in car/vehicle, motorcycle etc catalytic converter.
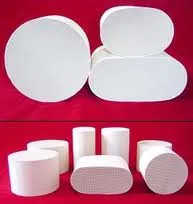
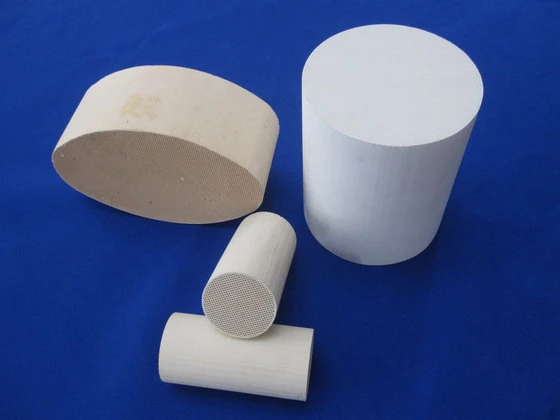
Specification
*Density: 1.7~3.8g/cm3
*Thermal expansivity: 1.5~5.0× 10-6/° C(20~100° C)
*Thermal conductivity: 1.2~3.0w/m. K(20~1000° C)
*Wall thickness: 0.8~1.5mm
*Compression strength: >50Mpa
*Heat exchange surface normal temperature: 300~500m2/m3
*Max Temperature: 1300~1400° C
*High working temperature
*Large specifc surface area
*Good thermal conductivity
*All shapes avalible
Application
*As support of catalyst, ceramic honeycomb materials are typically used for purifying automotive emission, removing bad smell etc, for instance, utilized in exhaust catalytic converter, air- fresher machine for hotel, restaurant, toilet and so on.
*Heat transfer agent: It can save 12% of energy in heat exchange, and it mainly utilized in heat recovery unit of RTO. Refractory stove: Low mass/volume, fast heat conduction. Gas burn distributing plate: Complete burn, energy saving is 10%.
*As filtrate substrate, they are generally utilized in food processing, environmental industry, metallurgical industry etc. For filtering particulate in industrial waste gas and bubble in liquid of molten melt and making the molten melt laminar so as to increase casting yields, also filtering impurities in juice, dextrose and sucrose etc.
Features:
*low thermal expansion
*large specific heat capacity
*high specific surface area
*low pressure drop
*small thermal resistance
*good thermal conductivity
*good heat-shock resisting ability
Item Type | Alumina | Mullite | Dense Cordierite | Porous Cordierite | Mullite - Cordierite | Stoneware | ||||||||
Chemical composition , % | Al 2 O 3 | 48~55 | 66~72 | 32~36 | 32~37 | 55~65 | 20~26 | |||||||
SiO 2 | 40~45 | 25~30 | 45~52 | 46~52 | 28~36 | 68~75 | ||||||||
MgO | / | / | 5~8 | 8~12 | 2.5~3.2 | 0.2~0.3 | ||||||||
K 2 O+NaO 2 +CaO | 4.0~5.5 | ≤ 1.0 | ≤ 3.0 | ≤ 2.0 | ≤ 1.0 | 2.5~4.0 | ||||||||
Density , g / cm 3 | 2.7 | 2.9 | 2.4~2.6 | 1.9~2.0 | 2.9~3.2 | 2.3~2.5 | ||||||||
Coefficient of thermal expansion (20~1000), × 10-6. | 5~7 | 5.5~6.5 | 2.5~3.5 | 1.3~2.5 | 2.5~4.0 | 5~7 | ||||||||
Heat capacity (20~1000),J/kg. | 800~900 | 1100~1300 | 800~1200 | 750~900 | 850~1100 | 840~920 | ||||||||
Thermal Conductivity (20~1000),W/m. | 1.5~2.5 | 1.5~2.0 | 1.5~2.5 | 1.3~1.5 | 1.5~2.3 | 1.0~1.2 | ||||||||
Spalling resistance. | ≥ 150 | ≥ 350 | ≥ 250 | ≥ 360 | ≥ 250 | ≥ 150 | ||||||||
Max. Working temp. | 1300 | 1600 | 1300 | 1300 | 1400 | 1300 |